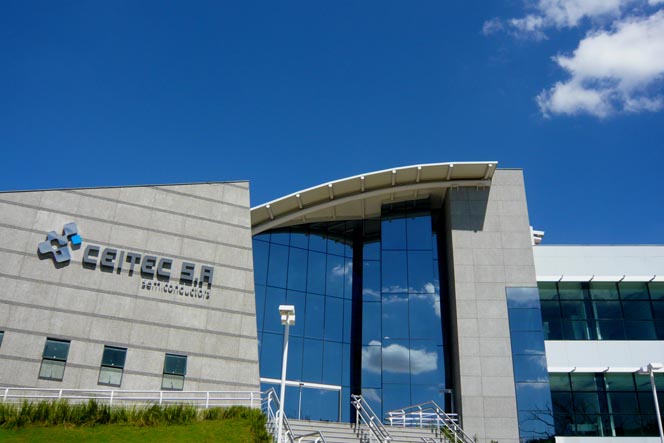
Techmundo
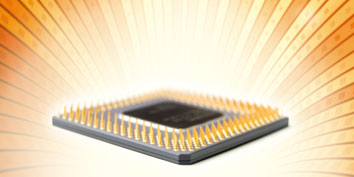
Luciano De Sampaio5 Compartilharam0 Comentários
Independente de ser utilizado como processador ou para armazenagem de dados, os chips de silício são cada vez mais onipresentes no dia a dia das pessoas. Desde seu celular até seu computador – passando por iPod, pendrive e câmera digital – todos esses aparelhos utilizam pelo menos um chip de silício.
Apesar de diferenças estruturais significativas, a produção de chips para processamento de dados ou armazenagem de informação é muito semelhante. Ambos os produtos surgem de wafers (bolachas, em tradução direta) de silício tratadas com pigmentos, esculpidas quimicamente e recortadas ao final do processo.
A fantástica fábrica de wafers
No começo de fevereiro de 2010 a IM Flash Technologies – joint venture da Intel e da Micron Technologies – abriu as portas da sua fábrica em Lehi, Utah, para diversos membros da imprensa.
A IMFT Lehi é uma fábrica exclusivamente dedicada à produção de memória NAND Flash, mas como o processo produtivo de wafers não difere muito, o local servirá de exemplo neste artigo.
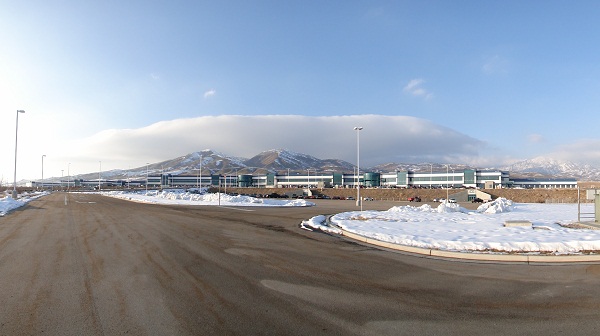
O prédio da IMFT Lehi é enorme, e como você pode conferir, fica num cenário de montanha de dar inveja. Aliás, vale lembrar: as fotos utilizadas neste artigo são de autoria do pessoal do PC Perspective, um dos blogs convidados a visitar a fábrica durante sua instalação e início da produção.
Tecnologia além do chip
O prédio da fábrica é um show à parte. Toda a estrutura é mantida nos pilares dos andares mais baixos, e nenhuma parede interna do andar ocupado – Cleanroom “Ballroom Fab” na imagem abaixo – suporta carga, servindo apenas como divisórias de ambientes.
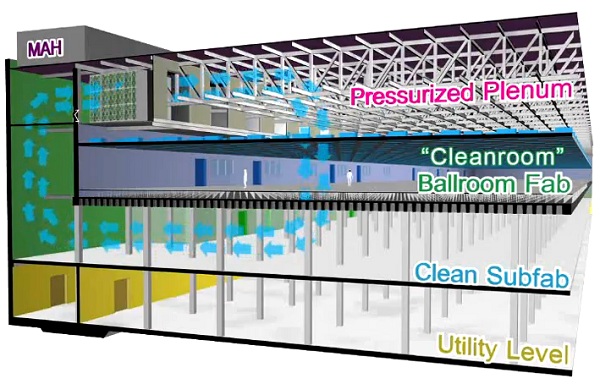
Com isso, o andar principal torna-se um enorme salão de vão livre. Nele os operários transitam, operam equipamentos e carregam informação para o maquinário espalhado nos andares inferiores – Clean Subfab e Utility level.
Um ponto importante – e bastante interessante – do processo de fabricação é que, em nenhum momento, os operários entram em contato direto com os wafers de silício. Mesmo assim as normas de operação exigem que os funcionários utilizem máscaras completas – deixando apenas os olhos descobertos – e roupas especiais para evitar a contaminação por partículas na fábrica.
Na foto ao lado você percebe que o assoalho do andar é todo perfurado. Isso é mais uma providência tomada para impedir a contaminação por poeiras e outras partículas no ambiente da fábrica.
Como a temperatura e a umidade do ar são controladas, a engenharia dos andares utiliza o próprio ar-condicionado para gerar um fluxo descendente, carregando pó e qualquer outro elemento estranho para o andar mais baixo do prédio, onde apenas serviços de manutenção são desempenhados.
Todo o material produzido é manuseado por máquinas. Robôs programados carregam os FOUP (Front Opening Unified Pod – cartucho unificado aberto pela frente) com as bolachas pelas diversas estações de fabricação, fazendo com que o trabalho humano seja principalmente de manutenção, acompanhamento e resolução de problemas.
Ensopado e churrasco
O processo de obtenção dos wafers é relativamente simples. Antes de tudo é necessário se obter silício – um dos principais componentes da areia. Obviamente determinados tipos de areia contêm um percentual maior de silício em sua composição, o que os torna ideais para a obtenção do material.
Com a areia correta carregada, além de alguns outros elementos necessários para a obtenção das propriedades elétricas necessárias a um chip de computador, cria-se um melt ao derreter a mistura de areia e outras cargas.
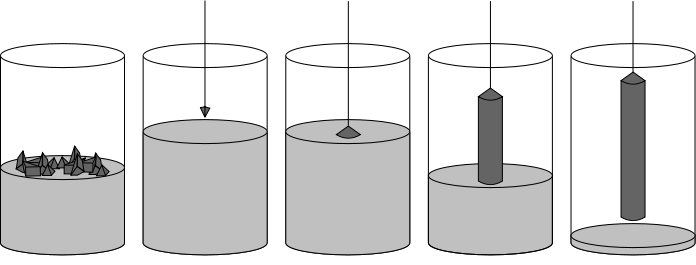
Pronto o melt, aplica-se um cristal de silício extremamente puro (em torno de 99,99% de silício) e sem falhas estruturais. O silício presente no melt se agrupa em torno deste cristal quase puro, formando uma barra de silício com praticamente a mesma pureza – com uma parcela mínima dos aditivos usados na mistura inicial.
Quando a barra de silício já tem tamanho suficiente, ela é retirada e levada para o corte. Os wafers são fatias transversais da barra cristalina, mais ou menos como um churrasqueiro faz com uma linguiça.
Da bolacha à lasca
Com o wafer recortado, o disco de cristal de silício passa por uma série de ajustes visando remover imperfeições e preparar a superfície para a impressão dos circuitos.
Depois de ter sua face polida, cada bolacha recebe várias camadas de pigmentos e outras substâncias químicas. Essas camadas extras receberão a impressão do circuito responsável pelo funcionamento do chip.
Essa impressão é feita de maneira semelhante a uma gravura, em um processo chamado fotolitografia. O desenho dos circuitos é criado em uma máscara – em um tamanho bem maior do que o do chip – e projetado através de lentes sobre as camadas que foram adicionadas depois do polimento.
Os locais onde a luz incide sobre o wafer são impressionados pela luz – não muito diferente do que acontece em uma fotografia – e tratados com agentes químicos para remover as partes indesejadas no circuito. Essa é a impressão dos caminhos dos elétrons.
Perceba que um wafer hoje considerado como estado da arte tem 300 mm de diâmetro – o próximo passo é aumentar essa medida para 450 mm – e chips de computador são muito menores do que isso. Cada disco recebe a impressão de vários chips, que serão posteriormente destacados e destinados às embalagens escuras que você encontra dentro da sua máquina.
Cada wafer é dividido, através da impressão dos circuitos, em dies – a área correspondente ao espaço ocupado por um elemento do circuito. No caso das bolachas de 300 mm utilizadas hoje, um único disco pode entregar até bilhões de dies.
Nem todos os dies são funcionais, entretanto. Contando o espaço de manipulação pelas máquinas, as áreas com informação de produção e falhas de impressão ou deposição de camadas, uma parcela de cada wafer é desperdiçada.
Como cada die não forma um circuito completo, esses bilhões de espaços tornam-se milhares – e em alguns casos apenas centenas – de chips. Depois de completado o processo de impressão, os chips são recortados do wafer e embalados em plástico para receber seu destino final.
Os chips criados por esse processo – como já foi dito antes – são utilizados tanto em processadores como em memória flash. O que diferencia um do outro são o tamanho final – chips de memória têm um formato padrão, o que não acontece com processadores – e o circuito impresso na etapa da fotolitografia .
O pessoal do PC Perspective colocou uma comparação interessante entre os tamanhos dos dois tipos de chip, que você confere nas fotos a seguir. Perceba que os chips de memória são bem menores que os de processadores (a moeda de quarter – à esquerda – tem aproximadamente o tamanho da moeda de 50 centavos brasileira, enquanto a de cent – à direita – tem o tamanho da nossa moeda de 1 centavo).
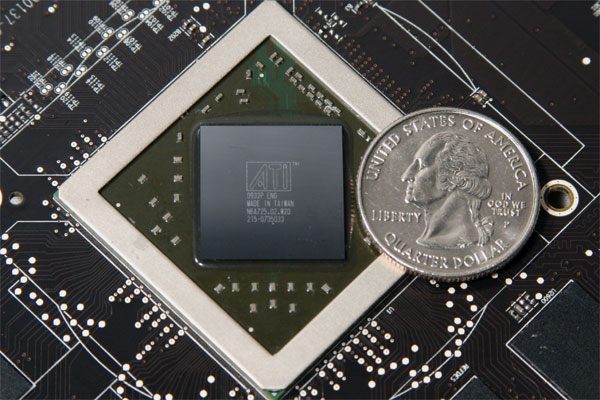
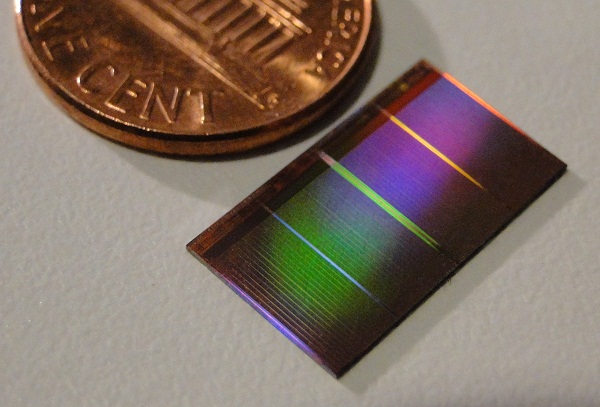
Saindo da fábrica
No total, o processo de fabricação de um chip – da extração do silício até as ligações elétricas e acondicionamento em plástico – dura duas semanas. A IMFT Lehi, ao atingir sua capacidade máxima de produção, fabricará dois mil chips por dia, prontos para a venda a empresas como a Intel e a Micron.
Dentro de cada computador, celular, MP3 player ou praticamente qualquer equipamento que você utiliza está – pelo menos – um desses componentes. Agora você já sabe toda a jornada que faz com que areia se torne um eletrônico refinado e de altíssima tecnologia.
Nenhum comentário:
Postar um comentário